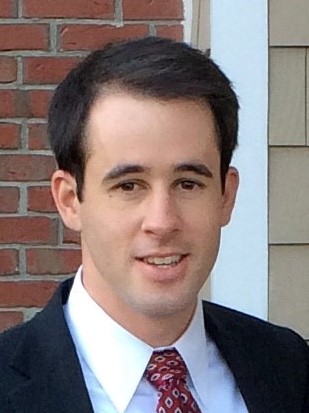
Progressive AM methods for fast-tracking a tool's path to market
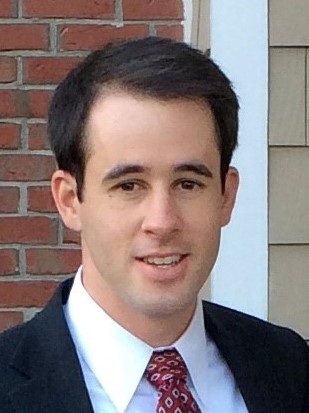
Advances in 3D printing applied sciences and development methods have enabled medical gadget producers to speed up innovation – from idea to commercialization. Additive manufacturing (AM) has change into extra cost-competitive versus conventional manufacturing because of new, extra environment friendly 3D printers, expanded materials choices, confirmed validation processes, software program with deep studying algorithms, regulatory grasp information and extra. The size in AM's favor is the flexibility to design extra advanced gadgets, combine lattice buildings to help bone progress, customise and even personalize gadgets, and scale up and down in response to reducing demand.
In terms of accelerating gadget improvement and approval, two key elements have demonstrated the best affect: 1) customer-focused consultants and a couple of) a well-defined, well-tested workflow. As medical gadget producers contemplate integrating AM into their manufacturing workflow, there are a number of necessary steps on the highway to market. For profitable AM implementation, you will need to absolutely perceive the targets of the brand new implant and/or gadget, and what the appropriate resolution can be to provide the gadget most successfully. Let's check out what you may anticipate:
1. Determine the necessity
A deep understanding of the applying is essential for effectivity and finally a profitable launch. It is very important spend time up entrance conducting thorough screening and evaluation to make sure there’s a enterprise case for additive manufacturing and to formulate a plan for design and improvement.
2. Collaborative innovation
On this section, the processes are tailored to the targets outlined for the gadget. The suitable expertise and materials are then chosen for the applying and the design is optimized. 3D fashions are accomplished and development optimization plans are drawn up.
3. Pre-prototype/prototype
Stacking development methods for implants reminiscent of acetabular cups assist reduce materials waste whereas rising productiveness by decreasing development occasions and post-processing steps.
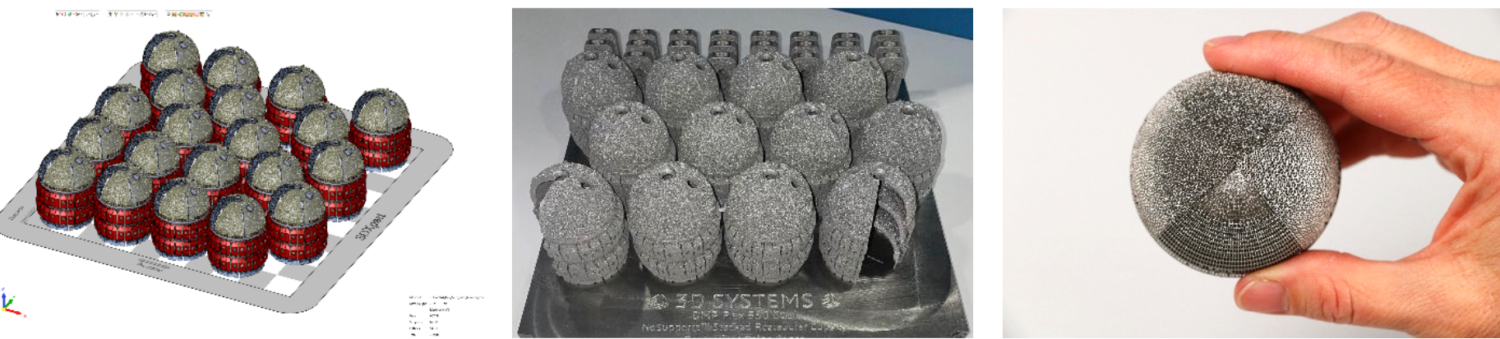
4. Low quantity manufacturing
Throughout this section, the gadget is examined towards a set of predefined validation and qualification standards to make sure the producer has all the information mandatory for submission and to drive market acceptance as soon as approval is acquired. It’s at this level that the producer appears on the path to scale up manufacturing.
5. Full manufacturing or expertise switch
This type of flexibility permits gadget producers to observe the trail that makes probably the most sense for them and helps speed up the funding in additive manufacturing options, but additionally cut back danger.
Go from innovation to FDA submission in simply 90 days
The standard time-frame for engineering groups to maneuver their orthopedic gadget improvements from market evaluation and prototyping to documentation and submission is twelve months to 2 years. The business accepted common is 20 months. But each month of delay will increase the dangers of escalating prices and shifting calls for in at the moment's fast-growing medical gadget business. The important thing to considerably decreasing ideation and validation occasions and accelerating income is partnership. Medical gadget producers contemplating integrating AM to provide gadgets are advisable to companion with an organization that may present not solely expertise options but additionally experience in medical gadget manufacturing and approval. Partnerships like these will help make the trail to market as fast and straightforward as doable.
About Ross Attardo
With practically a decade as an engineer in healthcare 3D printing, Ross Attardo is now an skilled guide managing product realization at 3D Methods' Software Innovation Group. Leveraging a wealth of information from his earlier roles at Johnson & Johnson, Attardo leads design, improvement and manufacturing initiatives for varied medical gadget purposes, making certain wonderful high quality and fast supply.